Non-Destructive Testing
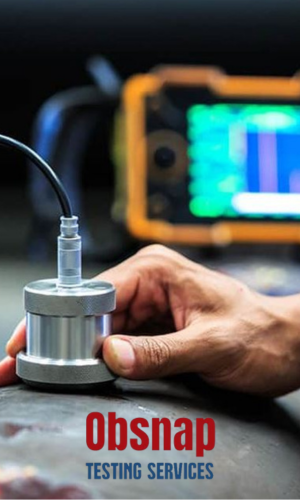
What is Non-Destructive Testing?
Non-Destructive Testing (NDT) is an expansive domain of analysis techniques meticulously engineered to evaluate the properties of materials, components, or systems without inducing any alteration or damage to their structural integrity. NDT methods encompass a diverse array of sophisticated approaches tailored to detect defects, measure material properties, and ascertain the integrity and reliability of structures and components across myriad industries. The significance of non-destructive testing cannot be overstated, as it plays an indispensable role in maintaining safety, quality, cost efficiency, regulatory compliance, and the extended service life of critical infrastructure and assets.
Why is this Non-Destructive Testing important?
Non-Destructive Testing (NDT) holds paramount importance for numerous reasons:
- Safety Assurance: NDT ensures that critical components and structures are free from defects that could potentially lead to catastrophic failures, thereby safeguarding human lives, preserving environmental integrity, and averting economic losses.
- Quality Control: By meticulously verifying that materials and products meet stringent specifications and standards, NDT safeguards the integrity and reliability of manufactured goods, fostering consumer trust, and enhancing brand reputation.
- Cost Efficiency: By adeptly detecting defects early in the production or operational lifecycle, NDT minimizes the cost of repairs, maintenance, and replacements, mitigating downtime, maximizing productivity, and optimizing resource utilization.
- Compliance with Regulations: NDT plays a pivotal role in facilitating compliance with rigorous industry standards and governmental regulations, ensuring that materials, components, and systems adhere to requisite safety and performance benchmarks.
- Extended Service Life: By facilitating continuous monitoring, assessment, and maintenance of equipment and structures, NDT prolongs their service life, enhances operational efficiency, and minimizes the risk of premature failures, thereby maximizing return on investment.
The foundational principle of Non-Destructive Testing (NDT) revolves around deploying an extensive array of techniques to inspect and analyze materials, components, or systems without incurring any alteration or damage to their structural integrity.
Key theoretical underpinnings encompassed in NDT include:
- Ultrasonic Testing (UT): Harnesses high-frequency sound waves to meticulously scrutinize the internal structure of materials, leveraging the reflection, transmission, and attenuation of ultrasonic waves to identify and characterize internal flaws, defects, or discontinuities.
- Radiographic Testing (RT): Exploits the penetrating power of X-rays or gamma rays to meticulously examine the internal features, defects, or inconsistencies within materials, elucidating variations in radiation absorption to generate high-fidelity radiographic images.
- Magnetic Particle Testing (MT): Capitalizes on the inherent magnetic properties of ferromagnetic materials to detect and delineate surface and near-surface defects or anomalies, employing magnetic fields and finely dispersed ferromagnetic particles to render defect sites discernible.
- Dye Penetrant Testing (PT): Relies on the capillary action of liquid penetrants to infiltrate surface-breaking defects or cracks in materials, subsequently employing developer agents to draw out and visualize the penetrant, enabling precise detection and characterization of surface flaws.
- Eddy Current Testing (ECT): Harnesses electromagnetic induction to induce eddy currents within conductive materials, scrutinizing variations in electrical conductivity or magnetic permeability to discern subsurface defects, material inconsistencies, or structural abnormalities.
An extensive arsenal of sophisticated tools and instruments is deployed in Non-Destructive Testing (NDT) to execute inspections with precision, accuracy, and efficiency.
- Prominent tools encompass: Ultrasonic Flaw Detectors: State-of-the-art instruments meticulously engineered to generate, transmit, and receive ultrasonic waves for flaw detection within materials, equipped with advanced signal processing capabilities to analyze waveforms and discern defect characteristics.
- Radiographic Equipment: Cutting-edge apparatuses encompassing X-ray or gamma-ray sources and detectors meticulously configured to produce high-resolution radiographic images, meticulously elucidating internal structures, defects, or inconsistencies within materials.
- Magnetic Particle Testing Kits: Comprehensive toolkits featuring magnetic yokes, finely dispersed ferromagnetic particles, and UV lights optimized for conducting magnetic particle inspections, facilitating the precise detection and delineation of surface and near-surface defects in ferromagnetic materials.
- Dye Penetrant Kits: All-inclusive packages comprising penetrant dyes, developer agents, and cleaning solutions meticulously formulated for conducting dye penetrant inspections, enabling the meticulous detection and characterization of surface flaws or discontinuities across diverse materials.
- Eddy Current Testers: Cutting-edge instruments meticulously outfitted with sophisticated eddy current probes, signal processing algorithms, and intuitive user interfaces for executing high-resolution inspections of conductive materials, adeptly discerning subsurface defects, material inconsistencies, or structural abnormalities.
Meticulously executing Non-Destructive Testing (NDT) mandates meticulous planning, preparation, and execution to ensure accurate, reliable, and reproducible results.
The overarching procedure encompasses:
- Preparation: Assiduously clean the test surface and meticulously set up the NDT equipment in strict accordance with the prescribed methodologies and specifications.
- Application of Technique: Ultrasonic Testing: judiciously apply a suitable couplant to ensure optimal acoustic coupling, systematically scan the material surface using an ultrasonic probe, meticulously analyzing waveforms to detect and characterize internal flaws, defects, or discontinuities.
- Radiographic Testing: Prudently position the material specimen between the radiation source and detector, meticulously expose it to radiation to generate radiographic images capturing internal structures, defects, or inconsistencies, meticulously interpreting radiographs to discern defect characteristics and locations.
- Magnetic Particle Testing: Meticulously magnetize the material specimen using a yoke or coil, meticulously apply finely dispersed ferromagnetic particles to the surface, meticulously inspect under UV light to discern defect indications, meticulously interpreting indications to ascertain defect characteristics and significance.
- Dye Penetrant Testing: Prudently apply the penetrant to the material surface, judiciously allow it to dwell and infiltrate surface discontinuities, meticulously remove excess penetrant, judiciously apply developer agents to draw out penetrant indications, meticulously inspect for defect indications, meticulously interpreting findings to discern defect characteristics and significance.
- Eddy Current Testing: Systematically scan the material surface using an eddy current probe, meticulously monitor and analyze resulting signals for indications of subsurface defects, material inconsistencies, or structural abnormalities, meticulously interpreting findings to ascertain defect characteristics and significance.
- Data Collection and Analysis: Diligently record and meticulously analyze data obtained during the inspection, judiciously interpreting findings to discern defect characteristics, significance, and potential implications.
- Reporting Results: Methodically compile comprehensive reports documenting the inspection procedure, meticulously summarizing observed indications, data analysis, and meticulously outlining any recommended actions, follow-up inspections, or mitigation measures.
Standards for Non-Destructive Testing Non-Destructive Testing (NDT) adheres to stringent international standards and guidelines to ensure consistency, reliability, and accuracy across various applications. Key standards encompass:
- ASTM E1444: Standard Practice for Magnetic Particle Testing, providing comprehensive guidelines for conducting magnetic particle inspections and assessing material integrity.
- ASTM E165: Standard Practice for Liquid Penetrant Testing, offering detailed procedures and requirements for conducting dye penetrant inspections and evaluating surface discontinuities.
- ASTM E213: Standard Practice for Ultrasonic Testing of Metal Pipe and Tubing, delineating procedures and techniques for ultrasonic inspection of metallic components and structures.
- ISO 9712: Non-Destructive Testing—Qualification and Certification of NDT Personnel, establishing criteria for the qualification and certification of NDT personnel to ensure competency and proficiency.
- ASME Section V: Nondestructive Examination, comprising detailed specifications and guidelines for performing various NDT methods, including ultrasonic testing, radiographic testing, magnetic particle testing, dye penetrant testing, and eddy current testing.
These standards provide comprehensive guidance on procedures, equipment, personnel qualifications, and quality assurance measures to ensure the consistent and reliable execution of Non-Destructive Testing (NDT) across diverse industries and applications. Adhering to standardized practices and methodologies is essential for achieving accurate, reproducible results and maintaining the safety, integrity, and reliability of critical infrastructure and assets.
no testing available.