Hardness Measurement
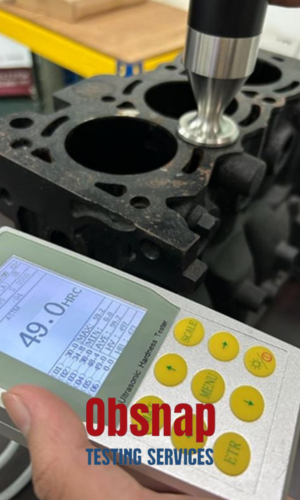
What is Hardness Measurement Testing?
Hardness testing is a method used to determine a material’s resistance to deformation, particularly permanent deformation, indentation, or scratching. Hardness testing provides valuable information about the material’s strength, wear resistance, and durability. Common hardness tests include Brinell hardness testing, Rockwell hardness testing, Vickers hardness testing, and Knoop hardness testing, each suited to different types of materials and applications.Hardness testing is a fundamental technique in materials science, engineering, and quality assurance. It plays a critical role in various industries such as aerospace, automotive, construction, and manufacturing, where understanding material properties is essential for product design, quality control, and performance evaluation. Hardness testing helps in assessing material performance and suitability for different conditions and applications.
Why is this Hardness Measurement Testing important?
Hardness testing is essential for several reasons:
- Material Selection : Hardness testing helps in choosing the appropriate material for specific applications based on hardness. It ensures that the material will perform as expected under operational conditions, enhancing product reliability and lifespan. Hardness testing provides critical data for engineers to select materials that meet the mechanical requirements of a given application.
- Quality Control : Hardness testing ensures materials meet required hardness specifications and standards. It helps manufacturers maintain consistent product quality and avoid defects, reducing the risk of failure and recalls. Regular hardness testing during production ensures that materials and products conform to design specifications.
- Predictive Maintenance : Hardness testing identifies potential wear and deformation issues in materials used in machinery and structures. This allows for proactive maintenance and prevention of equipment failure, thereby minimizing downtime and repair costs. Hardness testing is an important tool in maintenance schedules, helping to predict and prevent catastrophic failures.
- Research and Development : Hardness testing aids in the development of new materials and coatings with desired hardness properties. It supports innovation in creating materials with enhanced performance characteristics, such as increased strength, durability, and resistance to wear and corrosion. Hardness testing is crucial in experimental research to characterize and improve new materials.
- Compliance with Standards : Hardness testing ensures that materials comply with industry and governmental regulations. It provides a standardized method for verifying material properties, ensuring safety, reliability, and regulatory compliance in various applications. Adhering to hardness testing standards is vital for product certification and market acceptance.
The principle behind hardness testing involves pressing an indenter into the material’s surface under a specific load and measuring the resulting indentation. The size or depth of the indentation correlates with the material’s hardness. Key concepts in hardness testing include:
- Indentation Hardness : The resistance of a material to indentation, measured by the size or depth of the indentation left by an indenter during hardness testing. This provides a quantitative measure of the material’s hardness, which is crucial for assessing its suitability for various applications.
- Indenters : Tools made of hard materials, such as diamond or carbide, used to press into the material being tested. The shape and material of the indenter vary depending on the hardness testing method. Different indenters are used for different hardness testing methods, such as balls for Brinell, cones for Rockwell, and pyramids for Vickers and Knoop tests.
- Load Application : A specific force is applied to the indenter, and the resulting indentation is measured to determine hardness during hardness testing. The applied load and the duration of the load are critical parameters that influence the test results, requiring precise control to ensure accuracy and repeatability.
Brinell Hardness Tester : Uses a hard steel or carbide ball indenter and measures the diameter of the indentation during hardness testing. It is suitable for testing large, coarse-grained materials like cast iron and non-ferrous metals. The Brinell hardness number (BHN) is calculated by dividing the applied load by the surface area of the indentation.
Rockwell Hardness Tester : Uses either a diamond cone or a steel ball indenter and measures the depth of indentation under a major load during hardness testing. It provides quick and direct hardness readings and is widely used in industrial applications. Rockwell hardness values are represented by a scale letter (e.g., HRB, HRC) that indicates the indenter type and load.
Vickers Hardness Tester : Uses a diamond pyramid indenter and measures the diagonal length of the indentation during hardness testing. It is suitable for testing all types of materials, including small and thin specimens. The Vickers hardness number (HV) is calculated by dividing the applied load by the surface area of the indentation, with adjustments for the pyramid geometry.
Knoop Hardness Tester : Uses an elongated diamond pyramid indenter and measures the long diagonal of the indentation, suitable for brittle materials and thin layers in hardness testing. It is often used for testing ceramics, glass, and coatings. The Knoop hardness number (HK) is calculated by dividing the applied load by the projected area of the indentation.
Portable Hardness Testers : Handy devices for on-site hardness testing using various methods such as ultrasonic or rebound techniques. These are useful for testing large or immovable parts and in field inspections. Portable testers provide a convenient means to assess material properties without the need for extensive sample preparation or transportation to a laboratory.
The procedure for hardness testing generally involves the following steps:
Sample Preparation : The material specimen is prepared with a smooth, flat surface for hardness testing. Proper preparation ensures accurate and consistent test results, as surface irregularities can affect the indentation and measurement. In hardness testing, meticulous sample preparation is crucial for obtaining reliable data.
Selecting the Indenter and Load : The appropriate indenter and load are selected based on the material type and hardness testing method. This selection is critical for obtaining valid and comparable results, as different materials and test methods require specific combinations of indenter and load. Proper selection is essential for accurate hardness testing.
Applying the Load : The indenter is pressed into the material’s surface with the specified load during hardness testing. The load is applied for a set duration to ensure proper indentation and prevent excessive deformation or damage to the indenter. Controlled load application is vital in hardness testing for consistent results.
Measuring the Indentation : The size or depth of the indentation is measured using a microscope or an optical system during hardness testing. Accurate measurement is essential for calculating the hardness value, and advanced imaging systems can enhance precision and repeatability. Measurement accuracy is a cornerstone of reliable hardness testing.
Calculating Hardness : The hardness value is calculated using the specific formula for the chosen hardness testing method. Different methods have different formulas, reflecting their unique approaches to measuring hardness. For example, Brinell hardness is calculated using the diameter of the indentation, while Rockwell hardness is based on the depth of the indentation. Calculation precision is crucial in hardness testing for valid results.
Reporting Results : The results are compiled into a report, detailing the hardness values and any relevant observations from the hardness testing. The report includes the test method, indenter type, load, and any deviations from standard procedures, providing a comprehensive record for quality control and traceability. Detailed reporting in hardness testing ensures data reliability and accountability.
Hardness testing adheres to various international standards to ensure consistency and accuracy. Some key standards in hardness testing include:
- ASTM E10 : Standard Test Method for Brinell Hardness of Metallic Materials. This standard specifies the procedure for performing Brinell hardness tests and calculating hardness values, ensuring reliable and reproducible results. ASTM E10 is essential for standardizing Brinell hardness testing.
- ASTM E18 : Standard Test Methods for Rockwell Hardness of Metallic Materials. This standard provides guidelines for conducting Rockwell hardness tests and interpreting results, covering various scales and indenters. ASTM E18 is critical for the consistency of Rockwell hardness testing.
- ASTM E92 : Standard Test Methods for Vickers Hardness and Knoop Hardness of Metallic Materials. This standard details the procedures for Vickers and Knoop hardness tests, including sample preparation, load application, and measurement techniques. ASTM E92 ensures accuracy in Vickers and Knoop hardness testing.
- ISO 6506 : Metallic Materials—Brinell Hardness Test. This international standard outlines the Brinell hardness testing method, ensuring uniformity in test results worldwide and facilitating comparison across different laboratories and industries. ISO 6506 standardizes Brinell hardness testing globally.
- ISO 6508 : Metallic Materials—Rockwell Hardness Test. This standard provides guidelines for Rockwell hardness testing, ensuring consistency and reliability across different laboratories and applications. It covers various Rockwell scales and specifies the requirements for testing equipment and procedures. ISO 6508 ensures the reliability of Rockwell hardness testing worldwide.
- ISO 6507 : Metallic Materials—Vickers Hardness Test. This standard specifies the Vickers hardness testing method, including detailed instructions for test procedures, data analysis, and reporting. It ensures that Vickers hardness tests are conducted consistently and accurately, providing reliable results for material characterization and quality control. ISO 6507 is crucial for global Vickers hardness testing consistency.
- ISO 4545 : Metallic Materials—Knoop Hardness Test. This standard outlines the Knoop hardness testing method, suitable for thin layers and brittle materials. It includes guidelines for sample preparation, load application, and indentation measurement, ensuring accurate and reproducible results for materials with specialized hardness requirements.
- ISO 4545 standardizes Knoop hardness testing procedures internationally.
These standards provide detailed guidelines on test procedures, sample preparation, and data analysis to ensure reliable and reproducible results in hardness testing. Compliance with these standards
no testing available.